В последнее время изделия, изготавливаемые из композиционных материалов методом намотки, нашли широкое применение во многих отраслях: в космических аппаратах и ракетах, в авиации, в химической промышленности благодаря своим уникальным химико-механическим характеристикам [1]. Существуют два метода намотки изделий: «сухой» и «мокрый». В настоящее время используются оба метода, хотя методом «мокрой» намотки изделия изготавливаются чаще.
До настоящего времени системы регулирования технологических параметров намотки строились с применением электроприводов постоянного тока с тиристорными регуляторами напряжения. Системы управления имели аналоговые контуры управления, что усложняло изготовление систем, их наладку, ограничивало функциональные возможности приводов. В настоящее время, в связи с совершенствованием технологии «мокрой» намотки к системам управления стали прикладываться более жесткие требования, требующие более быстродействующих приводов с возможностью их адаптации к изменяющимся режимам работы в процессе намотки. Изменились и регуляторы натяжения. Вместо простой «восьмерки» стали использоваться комбинированные регуляторы, включающие электропривод и пневматический или механический усилитель [2]. Такое решение позволило с одной стороны уменьшить мощность применяемого электропривода, с другой стороны повысить полосу пропускания системы. В силу указанных обстоятельств в ЮРГПУ(НПИ) была разработана система регулирования натяжения «мокрой» композиционной ленты с регулятором натяжения, оснащенным дополнительным пневматическим приводом, с использованием в качестве исполнительного электрического двигателя синхронный двигатель с системой векторного управления фирмы Siemens. Рассмотрим процесс «мокрой» намотки изделий. Схематически тракт намотки показан на рис. 1.
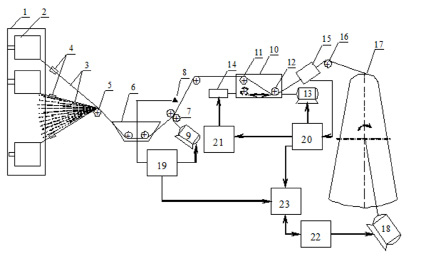
Рис. 1. Намотка изделий «мокрым» методом
На шпулярник 1 устанавливаются бобины с материалом 2. Количество бобин зависит от технологического процесса и может изменяться от 6 до 1200 штук. Сухой еще материал 3 проходит через натяжные устройства 4 и на специальной гребенке 5 формируется в ровницу. Долее ровница проходит через ванночку 6 со связующим. Количество связующего контролируется специальным датчиком 7. Избыток связующего удаляется отжимными роликами 8, зазор между которыми изменяется электроприводом 9. Натяжное устройство 10 состоит из неподвижного ролика 11 и ролика 12, перемещающегося вдоль натяжного устройства при помощи двух параллельно работающих приводов: электропривода 13 и пневмопривода 14. Таким образом, изменяется угол охвата «мокрой» лентой неподвижных роликов 11 и 12 и натяжение самой ленты. Натяжение ленты измеряется измерителем 15. Ролик 16 укладывает ленту на изделие 17 по специальной траектории. Для этого он снабжен механизмами укладки для простоты не показанными на рисунке. Изделие 17 приводится во вращение приводом 18. Отметим, что процессом намотки управляет несколько связанных друг с другом систем. Так процессом пропитки контролируется системой 19, процессом регулирования натяжения системами 20 и 21, процесс вращения изделия – системой 22. Блок 23 контролирует все параметры намотки и управляет ее процессом.
По своей технической структуре система управления построена двухуровневой. На верхнем уровне используется контроллер фирмы Siemens S7-300, на нижнем электропривод фирмы Siemens Sinamics S120. Функциональная схема приведена на рис. 2.
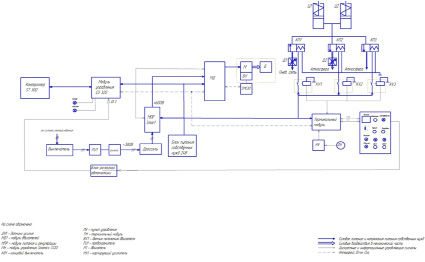
Рис. 2. Функциональная схема системы
Разработанная система управления способна обеспечить все специфические режимы работы технологического оборудования.
Рассмотрим особенности системы. Отметим, что для управления разработан специальный пульт управления ПУ, который связан с терминальным модулем ТМ 31. С помощью данного пульта можно задавать режимы работы привода («Заправка», «Автономно», работа в систему АСУ ТП «Автомат»). В режиме «Заправка» натяжное устройство автоматически переводится в положение, обеспечивающее минимальное натяжение материала. Это сделано для облегчения работы персонала в данном режиме. В режиме «Автомат» на контроллере верхнего уровня Siemens S7-300 собирается информация о технологическом процессе намотки. На основании этой информации контроллер формирует задание для работы станка. Отметим что, система управления натяжением может работать как под управление контроллера simatic S7-300 так и автономно. В последнем случае натяжения задается на пульте управления вручную и через терминальный модуль информация о заданном натяжении поступает на модуль двигателя МД. На индикаторе, установленном на ПУ, отображается установленное значение натяжения. Истинное значение определяется с помощью датчика усилия ДУ, сигнал которого через нормирующий усилитель НУ поступает на терминальный модуль. В нем имеется технологический регулятор – это ПИД регулятор, который используется для регулирования натяжения. Особенностью данной системы является переменный коэффициент усиления в зависимости от заданного значения натяжения. Использование переменного коэффициента позволяет повысить коэффициент усиления на малых натяжениях и улучшить точность отработки заданных значений натяжения во всем диапазоне работы системы. Отметим особенность системы – использование пневматического усилителя (цилиндра), работающего параллельно исполнительному двигателю. В зависимости от момента на валу электродвигателя терминальный модуль подключается одному из трех твердотельных реле KV1-KV3. При включении КV1 срабатывает электропневматический клапан КП1, который связан через дроссель ДР1 с пневматической сетью и при его срабатывании повышается давление в пневматических цилиндрах Ц1 и Ц2, тем самым, помогая электродвигателю перемещать исполнительный механизм натяжного устройства. При срабатывании второго твердотельного реле КV2 через электропневматический клапан КП2 и дроссель ДР2 давление в пневматических цилиндрах плавно уменьшается, что тоже помогает перемещать исполнительный механизм, но уже в другую сторону. При остановке станка и при нажатии кнопки «Заправка» на короткое время включается твердотельное реле KV3, осуществляющие быстрый сброс давления с пневматических цилиндров через электропневматический клапан КП3. Исполнительный механизм перемещается в исходное состояние, обеспечивается минимальное натяжение.
От системы электроснабжения питание подается на модуль питания и рекуперации МПР Smart с помощью выключателя QF, предохранителя FU, сетевых фильтра и дросселя. В свою очередь от МПР Smart через МД запитывается электродвигатель М1.
Работа привода в составе АСУ ТП практически мало отличается от описанной ранее, но уровень натяжения задается контроллером верхнего уровня. При этом привод обменивается с контроллером дополнительной информацией, необходимой для решения задач АСУ ТП.
Разработанная система прошла испытания в лабораторных условиях. Графики изменения натяжения, момента на валу двигателя, скорости вращения двигателя и сигналы управления клапанами пневматической системы показаны на рис. 3.
Из приведенных графиков видно, как на начальном участке задающее напряжения было равно 0Н. Значение натяжения, равное 300Н объясняется предварительным натяжением «мокрой» ленты. В конце участка на систему управления подается задающее воздействие, равное 2500Н. Момент на вале двигателя практически сразу достигает максимального значения и поддерживается на данном уровне некоторое время. Скорость двигателя нарастает до значения 500 рад/с и постепенно уменьшается. Данное явление объясняется увеличением сигнала обратной связи от датчика натяжения. Так как момент двигателя достигает максимального значения, включается в помощь пневматическая системы. Открывается клапан и в пневматические цилиндры нагнетается воздух, пневматические цилиндры «помогают» электродвигателю перемещать исполнительный механизм. В конце данного участка момент на валу двигателя уменьшается, электропневматический клапан выключается. На следующем участке момент двигателя не превышает максимального и электродвигатель работает самостоятельно, продолжая перемещать исполнительный механизм. Далее момент двигателя изменяется на противоположное значение. Это связано с избыточным давлением в пневматических цилиндрах, вызванное компенсацией динамических составляющих процесса. При этом натяжение практически не изменяется, оно стабилизировано на заданном уровне, а давление в пневматических цилиндрах уменьшается. Для этого включается специальный элетропнематический клапан. Скорость двигателя практически равна нулю, перемещение исполнительного механизма незначительные. Далее, идет стабилизация натяжения на участке намотки. Пневматические цилиндры в процессе работы не участвуют так как момент на валу двигателя не достигает максимального значения. Скорость вращения двигателя очень маленькая. В конце намотки подается управляющее напряжениие, соответствующее натяжению в 300Н. Момент на валу двигателя становится отрицательным и равным максимальному значению, включается элетропнематический клапан, окончательно сбрасывающий давление в пневматических цилиндрах. Исполнительный механизм перемещается в исходное положение.
Выводы: электропривод в комплексе с пневматической системой обеспечивает быстрое и качественное регулирования натяжения в заданном диапазоне. Пневматическая система помогает электродвигателю при превышении им заданного момента на валу, работают системы синхронно. В настоящее время система прошла приема – сдаточные испытания на заводе – изготовителе намоточного станка и монтируется на предприятии заказчика, где будет работать станок.
Рис. 3. Результаты лабораторных испытаний электропривода механизма намотки